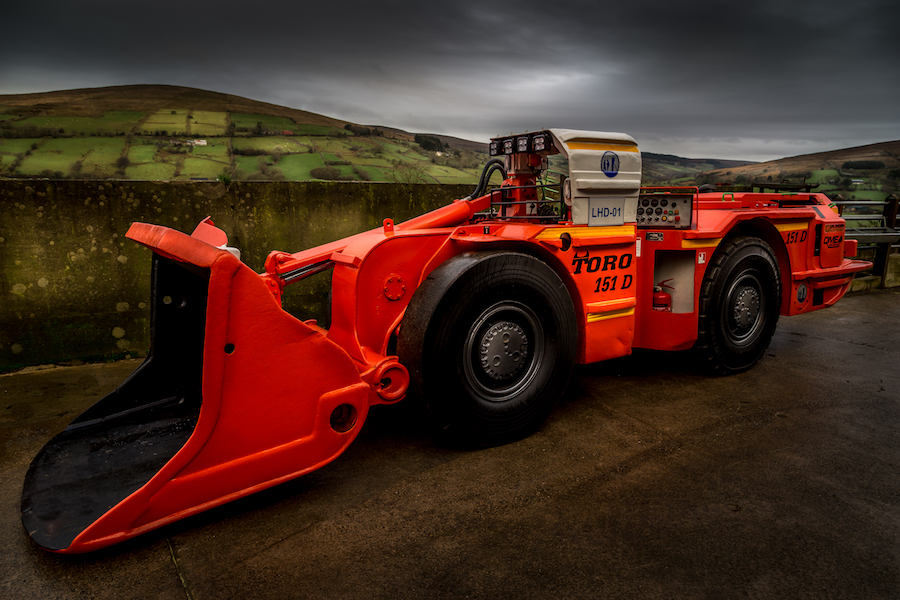
Article
How does a mine work?
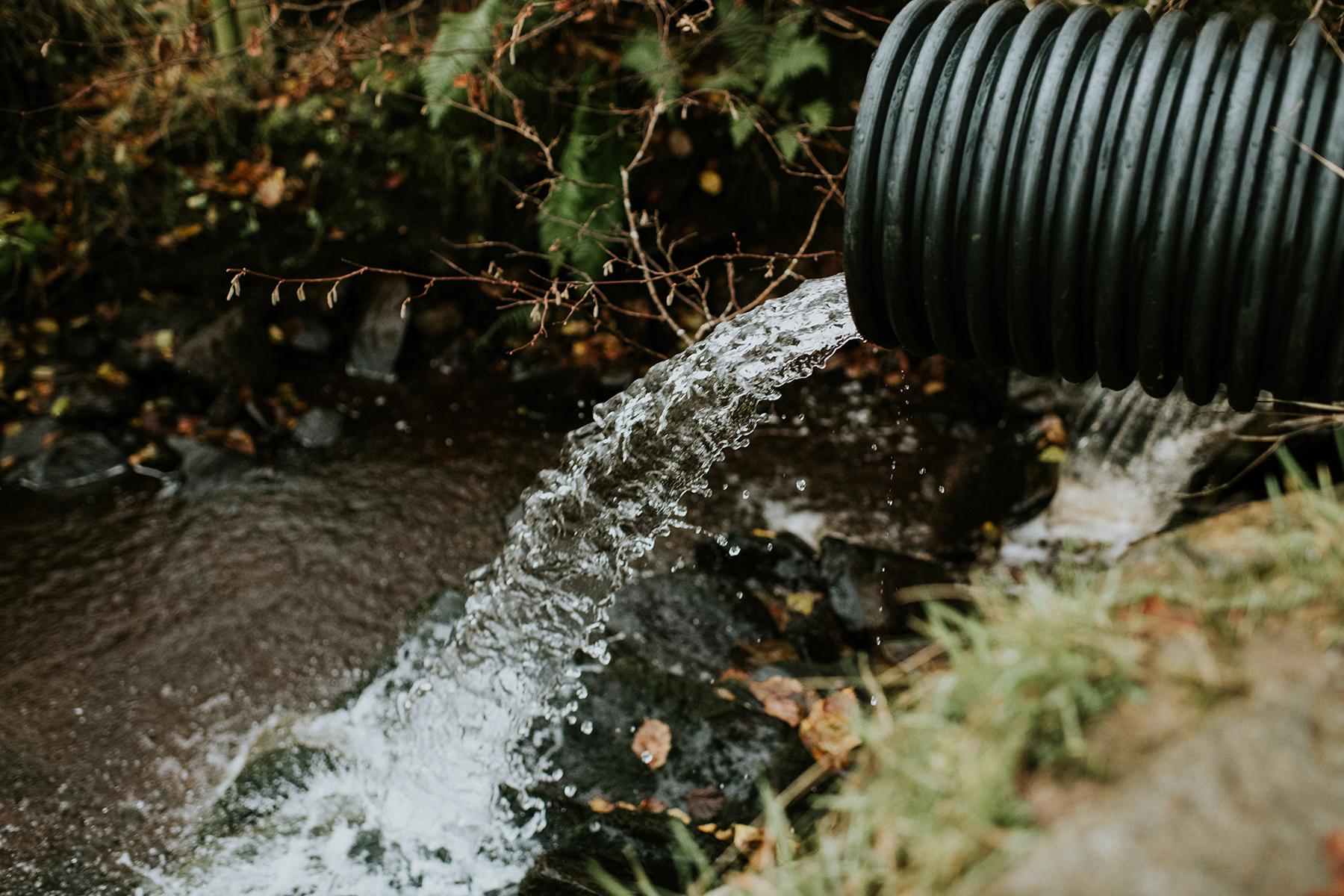
Six stages to unlocking Tyrone’s precious metals.
One of the most popular questions for our Community Relations team is ‘How does a mine work?’
Perhaps the best comparison is to think of Dalradian’s project as a hi-tech, highly regulated, precision-led quarry – only one that is below ground, with processing on the surface.
There are six stages to Dalradian’s environmentally responsible mining project: narrow-vein mining, processing, rock management, water treatment, shipping and refining, and rehabilitation.
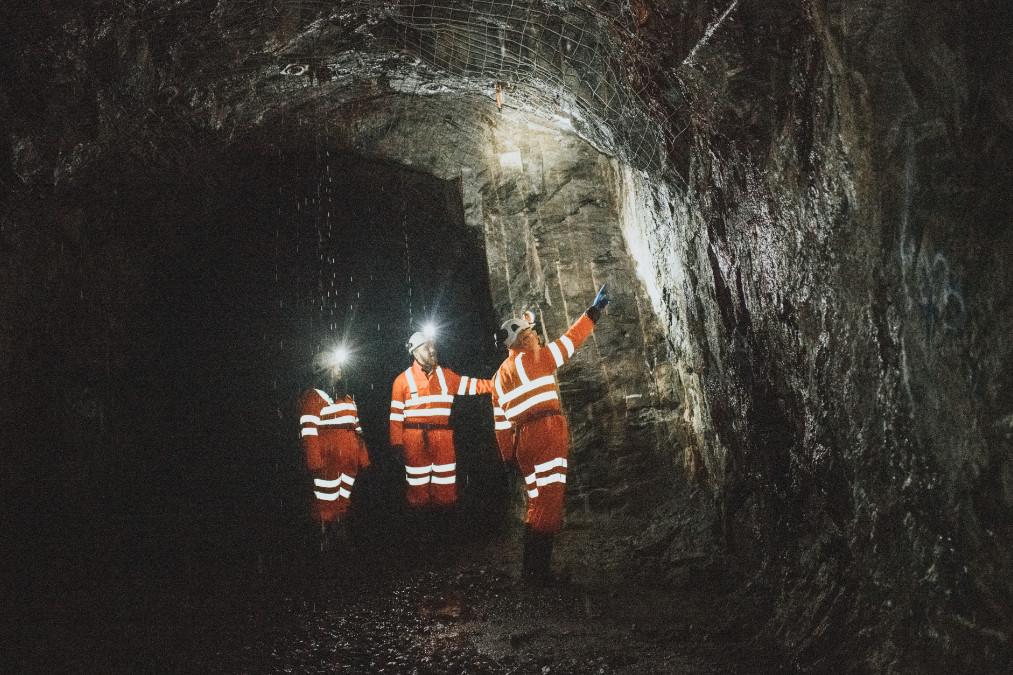
Narrow-vein mining
Unlocking Tyrone’s Precious Metals
All of Dalradian’s mining activity will take place underground using a technique known as narrow-vein mining, so called because of the narrow veins of quartz rock – roughly 1m in width – which contain Curraghinalt’s gold, copper and silver.
The objective is to systematically extract just these veins (sometimes called ‘ore-bearing rock’) while leaving as much of the ordinary ‘country’ rock in place as possible. This reduces the amount of mining and processing required, which minimises energy use.
Narrow-vein mining is a precision-led, largely mechanised process that uses drilling and sampling to build a computer model of the deposit to help identify which veins to mine first and where best to develop and blast using targeted explosive charges. Mining usually takes place from tunnels underneath the veins to allow gravity to provide a helping hand. The blasted ore-bearing rock or ‘muck’ is loaded into underground trucks using a LHD (load-haul-dump).
The mined ore-bearing rock will then move onto the next stage, processing, which will further separate the metals from the rock. The majority of extracted rock will remain underground to backfill the spaces created by mining.
The hi-tech nature of modern mining has greatly increased the amount of machinery which can be controlled remotely from an underground safe area or from the surface, helping support a safe work environment. Wi-fi will track where people are working underground, further enhancing safety and ensuring energy is used more efficiently.
With an initial £15m training programme, it is expected that the mining aspect of operations will involve approximately 250 of the project’s 350 direct employees, providing roles for, among others, miners, haul truck operators, mechanics, welders and electricians.

Processing
Unlocking Tyrone’s Precious Metals
Once the narrow veins which contain Curraghinalt’s gold, copper and silver have been mined underground, the next step is to separate the valuable minerals from the extracted rock. This ‘processing’ is mostly completed underground before moving to the surface for secondary processing.
Most extracted rock will not contain useful metals and one of the project’s guiding principles is to keep as much of this ‘barren’ rock as possible underground. This is environmental good practice, uses less energy, strengthens the mine development, and keeps the amount of rock stored above ground to a minimum.
Using a ‘crusher’ underground, the mined rock is broken down into smaller pieces (tennis ball sized or smaller). These crushed rocks are separated from the minerals using a specialised ‘ore sorter’ with sensors to detect higher density pieces containing gold, copper and silver.
To minimize carbon and dust emissions, a covered electric conveyor belt will transfer rock to the surface (this is a refinement of the original proposal which used diesel-fuelled trucks and will, with other measures, reduce fuel consumption by 25%).
The ore goes to the processing building above ground, whilst the remaining rock, devoid of minerals, is either retained underground to backfill spaces created by mining or stored above ground in a ‘Dry Stack Facility’ (DSF).
For secondary processing, the ore enters a two-stage grinding circuit in the processing building. The ore is rotated with steel balls and water in large “drums” to mill it into a finer size (similar to sand). It is then sent to a flotation tank.
Using just water (which is 80% recycled within the process) and biodegradable substances, the flotation tanks help metallic elements attach to bubbles which float to the top where they are skimmed off to form a mineral concentrate. The concentrate will be shipped to smelters located in Germany, Sweden or elsewhere to create gold and silver bars and copper sheets.
In response to community feedback, Dalradian changed the processing method in 2019 to remove the use of cyanide and therefore the need for a hazardous substances consent.
Due to Tyrone’s global leadership in designing and manufacturing mining and quarrying equipment, some processing equipment will be sourced locally.

Rock Management
A Best-in-Class Approach
Operations at Curraghinalt will mine two-types of rock – ‘ore’ which contains metals and ‘non-ore bearing rock’ which doesn’t.
The project is designed to retain as much non-ore bearing rock underground as possible. The remainder will be placed above ground in a DSF.
Rock is first processed underground through a crusher and an ore sorter. Ore is transported by an electric, covered conveyor to the surface for secondary processing. Non-ore bearing rock will be used to backfill tunnels and ensure that no large spaces are left underground. Some of this material will also help form the DSF’s outer layer.
On the surface ore is further processed, creating a concentrate containing valuable metals to be shipped overseas. The left-over rock is known as ‘tailings’. Just over half of these tailings will be pumped underground to be turned into a cement paste to backfill cavities. The remaining tailings will have most of their water removed before being sent to the DSF.
Traditionally, tailings would be stored as a semi-liquid in ‘wet tailings dams’. By using the latest DSF technology (acknowledged by the EU as a best available technique) there will be no ‘wet tailings dams’ at Curraghinalt.
The DSF is an engineered, designed feature which is smoothed, shaped and compacted safely and securely. Over the c.25-year life of mine, it will have an average thickness of c.17m and won’t contain acid-generating rock.
Located in a natural hollow, the DSF will be contoured and progressively planted during operations to help it further blend in with the surrounding area, much like a landscaped embankment. Dalradian’s Environmental Statement contains detailed plans for the DSF which are being reviewed by planners and their expert consultants.
Water draining from the DSF (typically rainwater) or any water which comes into contact with mine operations will be captured and treated in a state-of-the-art, reverse osmosis water treatment plant in line with strict regulatory standards.

Water Management
Improving Water Quality
Dalradian has proposed a sustainable approach to water management that meets stringent environmental and regulatory standards and, together with a water quality Betterment Plan, will improve the quality of water in the local area.
The underground gold-copper-silver mine will prioritise water recycling (c.80% within the processing plant) and minimise the use of fresh water. All water which comes into contact with operations will be captured, treated and monitored to meet independent, strict criteria set by the Northern Ireland Environment Agency.
Two major pieces of infrastructure will be built to achieve this. First, a state-of-the art water treatment plant that treats and discharges water to a high standard which is protective of aquatic life, and secondly, four ponds to capture rainfall and water from the site / operations.
The water treatment plant will use ultra-filtration and reverse osmosis water purification technology (including a semi-permeable membrane that removes ions, molecules and large particles). Apart from iron and manganese which occur naturally at elevated levels in local waterways, the water discharged will be cleaner than drinking water. Dalradian has proposed a Betterment Plan for its land holdings which, together with a very high standard of water treatment, will result in improving water quality in the rivers neighbouring the proposed mine site. The Betterment Plan includes measures such as tree planting, habitat enhancements and ceasing some agricultural practices.
One of the ponds will collect rainwater, some of which will be used in operations. The other three ponds will capture water that comes into contact with mining operations, including water from the underground mine and DSF.
The ponds will be excavated fully into the ground. They are not ‘dams’ and will not use water retaining embankments or dam walls. The ‘mine contact’ ponds are designed to contain a 1-in-a-1000-year, 24-hour storm event without overtopping.
All water in these ponds which isn’t reused in operations will be treated at the water treatment plant before being discharged.
Based upon extensive modelling and independent testing of over 1,000 samples, the proposed mine is designed to operate in tandem with the local environment. Water management is integral to that approach.

Shipping & Refining
Completing the transformation
During the planning process Dalradian listened to our local community and changed its proposals with the aim of becoming Europe’s first carbon neutral mine. We also reduced the amount of processing required at Curraghinalt by removing the use of cyanide. This means that the mineral concentrate produced by processing on site needs to be transported overseas to finalise the transformation of microscopic ore from the Sperrins into recognisable gold and silver bars, and copper sheets.
Although the final destination of the concentrate is still to be decided, there are a number of well-established smelters in continental Europe and North America which already process concentrate from around the world. To get there, sealed bags of concentrate in containers will leave Curraghinalt by road in covered lorries (around three a day) to a port where it will be shipped overseas. A similar approach is used by Tara Mines in Meath which ships its concentrate to Scandinavia.
Separating the concentrate into gold, silver and copper is achieved through ‘refining’, a process which traces its origins back thousands of years. Refining at modern smelters is, of course, much more sophisticated and highly regulated, but it is based on the same principles of using heat and other agents to remove impurities from the concentrate. This helps separate the concentrate into its valuable end products, each of which might undergo further specialist refining.
Dalradian’s proposal for Curraghinalt will produce 15,000 tonnes of copper, 3.5m ounces of gold and 1.7m ounces of silver over the 20-25 year life of the mine. The deposit also contains smaller amounts of materials on the UK and EU critical minerals lists – antimony, bismuth, cobalt and tellurium.
Gold, silver and copper are known for their usefulness in electrical circuits. Today they can be used in everything from mobile phones to laptops, electric vehicles and for medical purposes, as well as emerging renewables technology such as solar panels, which will be crucial to reducing global CO2 emissions.

Rehabilitation
Responsible mine closure is an opportunity for a positive legacy
Although mine operations may last up to 25 years, Dalradian has already submitted proposals to return the site to its present-day use in a Rehabilitation and Closure Plan. The plan will form the basis for a legal agreement with the Department for Infrastructure and which regulators / stakeholders will feed into. It will be regularly updated to take account of new technology and community views.
Rehabilitation is integral to the mine’s design and will start during operations. The DSF, for instance, will be progressively replanted with hedgerows and native species, and re-contoured to blend into the local landscape.
Some rehabilitation, i.e., removing underground equipment, can only occur after operations finish, but the objective is to return the land to farming, native woodland and moorland, as appropriate. Alternatively, the community may wish to retain and repurpose some buildings / infrastructure, create a nature reserve to enhance biodiversity and act as a carbon sink or support other sustainability projects. Most rehabilitation will be completed within one year after closure but monitoring to ensure that environmental requirements are met will continue.
Dalradian will provide a financial guarantee and set aside funds (in advance and agreed with Government) to cover all rehabilitation costs as is the case at our current exploration site.
We also want to leave a legacy that supports the wealth and health of our community. A good example of what can be achieved is Lisheen Mine, Co. Tipperary. When it closed in 2015 a carefully structured closure plan was initiated in consultation with local communities. €80m-worth of facilities were kept, helping establish a leading European bio-tech research hub.
Dalradian has committed a minimum of £4m to support community sustainability projects and a £15m training programme should operations proceed. With skills development and training, community investment, business start-ups and expansions, potential development of centres of excellence, and the option to repurpose above-ground infrastructure or create a nature reserve, who knows what opportunities the future will bring?
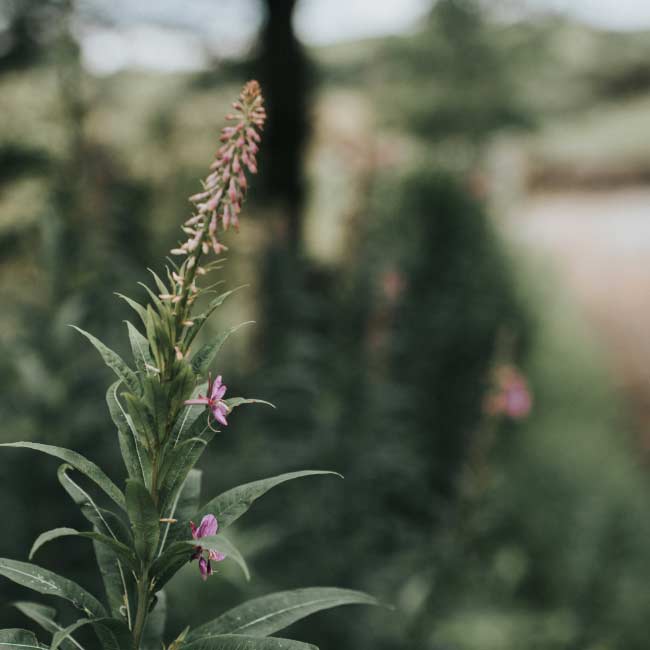
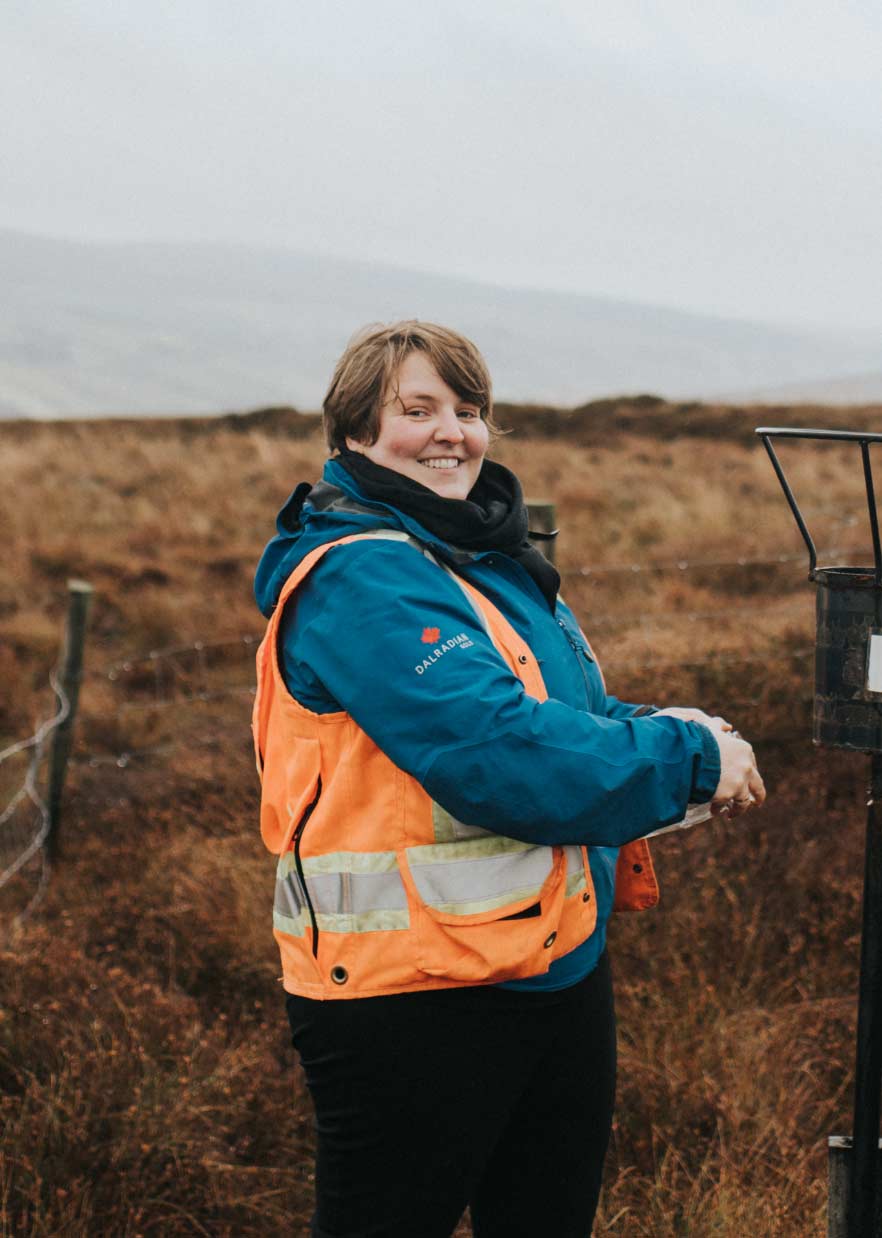
Your support matters
Support our plans to create jobs, strengthen the local community and respect the environment. The Department for Infrastructure will take your views into account. Help make our plans a reality.
Your letter of support will be sent directly to the Department for Infrastructure. Dalradian will not see your letter, nor any of your details.
Great things can happen with your support
Support our plans to create jobs, strengthen the local community and respect the environment. The Department for Infrastructure will take your views into account. Help make our plans a reality.
Customise a letter of support in two simple steps:
Provide your personal details
This will signal your support to the Department for Infrastructure. You can choose to keep these details private.
Tell the Department for Infrastructure why you support the project
Please tick all the elements you like about the proposed project.
Dalradian will not see your letter, nor any of your details. Your letter of support will be sent directly to the Department for Infrastructure